PRESS RELEASE: Australian Made App saves project $3.5million and keeps 25,000 employed
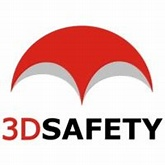
THE PROOF IS IN THE PUDDING: A NEW WAY WITH NORTHCONNEX
Connecting the M1 Motorway in Wahroonga to the Hills M2 Motorway with NorthConnex was no small feat. To get a rough idea of this project’s sheer scale, consider this: the twin tunnels, which opened in October 2020, are around nine kilometers long, with two 3.5-meter lanes and an additional break down lane. At 90 meters underground in some parts, it’s also Australia’s deepest tunnel and has a capacity of 100,000 vehicles each day.
To say it was a complex process is putting it mildly – and yet, by the end of the $3 billion project, those overseeing the creation of NorthConnex couldn’t speak highly enough of the involvement of 3D Safety, which streamlined everything from worker onboarding and online orientation to printing site-access cards and delivering paperless site inductions.
Using its fully tailorable tech, 3D Safety handled not only the setup and successful flow of employees onto the project, but also the management of authorisation and approval for workers to perform high-risk tasks, plant operation (including onboarding and spot auditing), and site access management across 26 sites and 59 zones.
The application also made it possible to deliver instant customised communication to the entire workforce – everything from staff notifications to emergency evacuation functions.
Within just the initial year of the five-year project, the 3D Safety application had more than paid for itself. “The investment in 3D Safety was recouped many times over within the first 12 months of the project,” reveals the NorthConnex safety director.
In fact, by the time the tunnels opened, the app’s capabilities for streamlining onboarding and induction processes for people and plants alone saved the project a whopping $3.5 million in admin time. Over the life of the job, “25,000 people worked on the project”, says 3D Safety director Simon Morrow. “In terms of delivering efficiencies, we were able to get someone, from the moment they walked onto the site, to start working two hours quicker because they’re not being slowed down by paperwork. They had already done their initial training online through the application, so they’re not sitting in a room doing a four-hour-long induction course when they arrive on day one. That’s two hours they saved – two additional hours of productivity.”
At around $100 per hour per worker, for 25,000 personnel, “We’re talking millions of dollars in productivity gains,” Simon adds.
Add to that an 80 percent reduction of the onboarding team needed over the life of the project – equalling $800,000 saved in payroll costs – and it’s clear the investment in 3D Safety was worth every cent.
3D Safety’s improved access to documentation and governance evidence during audits also improved industrial relations on site. “Where worker representatives were concerned about worker safety, we were able to look on our system and see easily where every worker was at any given time. If an incident occurred, project leaders knew with a few taps of a screen who to look for and where,” explains Simon. “The project teams could evacuate everyone quickly if the need arose and account for every worker very quickly. If someone needed to be contacted, that info was readily available, too.” With 3D Safety, issues around governance and compliance that would traditionally take weeks to sort out were resolved in record time. “The directors on the project told us they were able to close out issues in hours, not weeks because they had the critical up-to-date information at hand.”
As you can imagine, 3D Safety’s features also sped up the standard client auditing processes. “The nature of audit is very targeted questioning,” explains Simon. “If you can produce a response and an answer quickly, auditors move their focus because they’re satisfied.”
Ultimately, the results speak for themselves. Overall, the ROI on the NorthConnex project was estimated at >860% – an astonishing outcome for such a large-scale project. “We were proud to achieve such an incredible result for the client,” says Simon, “but, honestly, we weren’t surprised. Once our clients see how 3D Safety transforms their projects, the take-up, productivity gains, and insights they get are phenomenal.”
3DSafety director Simon Morrow and marketing manager Brett Sheridan are available for interview. To speak with them or learn about the application’s capabilities and proven results, contact Amanda Kuhn ([email protected]).
3dsafety.com.au
About 3DSafety.com.au
3D Safety is a leader in delivering safety compliance, systems, and processes to industry through our unique approach – People, Plant, and Process.
With over 30 years of delivering safety training, equipment, and services to Australian sites, 3D Safety is the market leader in the areas of compliance Management, Workplace Health and Safety, and industry-specific Safety Training.
3D Safety comprises a highly-skilled, highly experienced team of mobile staff that service the safety and compliance needs of more than 1,500 organisations across Australia.