PRESS RELEASE: From Cylinder to Cement Kiln: Tracking the Final Journey of Refrigerants
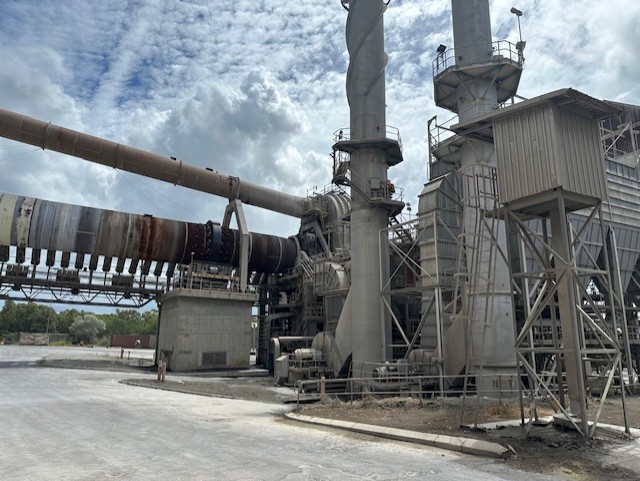
Most people don’t stop to think about what happens to refrigerant gas once it is no longer needed. However, for the team at Refrigerant Reclaim Australia (RRA), this end-of-life process is a critical piece of the puzzle for reducing greenhouse gas emissions and protecting the ozone layer. Recently, the RRA team went on a field trip to Cement Australia’s Gladstone facility to witness firsthand how refrigerant gases are safely and effectively destroyed.
From Recovery to Destruction: A Behind-the-Scenes Look
RRA is responsible for the collection and destruction of Australia’s recovered refrigerants, including CFCs, HCFCs HFCs, & HFO blends. These refrigerants are collected in various forms, from bulk vessels to small recovery cylinders from collection points across the country. Once collected, they are stored and processed at our facility before being transported to Gladstone for final destruction.
The Gladstone site, operated by Cement Australia, is no ordinary factory. It houses one of the most advanced facilities in the country, capable of thermally destroying ozone-depleting substances at extremely high temperatures.
Why Cement Kilns?
Cement kilns have a long history as industrial workhorses. They are traditionally used for producing clinker, a key component in cement, through extremely high-temperature combustion processes. Over time, their engineering and thermal properties have positioned them as suitable candidates for the destruction of high-global-warming-potential substances, including ozone-depleting substances (ODS) and hydrofluorocarbons (HFCs).
How the Process Works
At the facility, the prepared refrigerant is vaporised and injected directly into the main burner of the rotary cement kiln, typically near the flame zone. This is the hottest part of the kiln, where temperatures reach up to 1400 degrees. The extremely high thermal energy, combined with long residence times (how long the material remains at high temperature), ensures that the complex halogenated compounds in refrigerants are broken down at a molecular level. This results in Destruction and Removal Efficiencies (DRE) of up to 99.99 percent, well above international thresholds for safe disposal.
The alkaline environment within the kiln makes cement kilns uniquely suitable for this task, primarily due to the raw materials used for clinker production. When refrigerants are combusted, they can produce acidic by-products such as hydrogen fluoride (HF) or hydrogen chloride (HCl). However, these by-products react with the kiln’s lime-based material and are chemically neutralised, becoming part of the clinker. This eliminates the need for post-combustion residue handling, such as fly ash disposal, that is often required in conventional waste incineration.
Why it Matters
Refrigerants may be out of sight once they leave our air conditioners or refrigerating systems, chillers, and heat pumps but they pose a major environmental risk without proper management. Many refrigerants have global warming potentials thousands of times greater than carbon dioxide. If released into the atmosphere, even small quantities can have long-lasting impacts on the climate.
By partnering with Cement Australia, RRA ensures that harmful refrigerants are destroyed in a way that is both scientifically effective and environmentally responsible.
This partnership also sets an example of how industrial processes can contribute to circular economy principles and emissions reduction targets when guided by environmental responsibility.
Author: Stacey Kershaw-Brant