PRESS RELEASE: As Global Demand for Lithium Batteries Soar, Australia Takes a Hard Look at its Current Export Figures and Manufacturing Capabilities
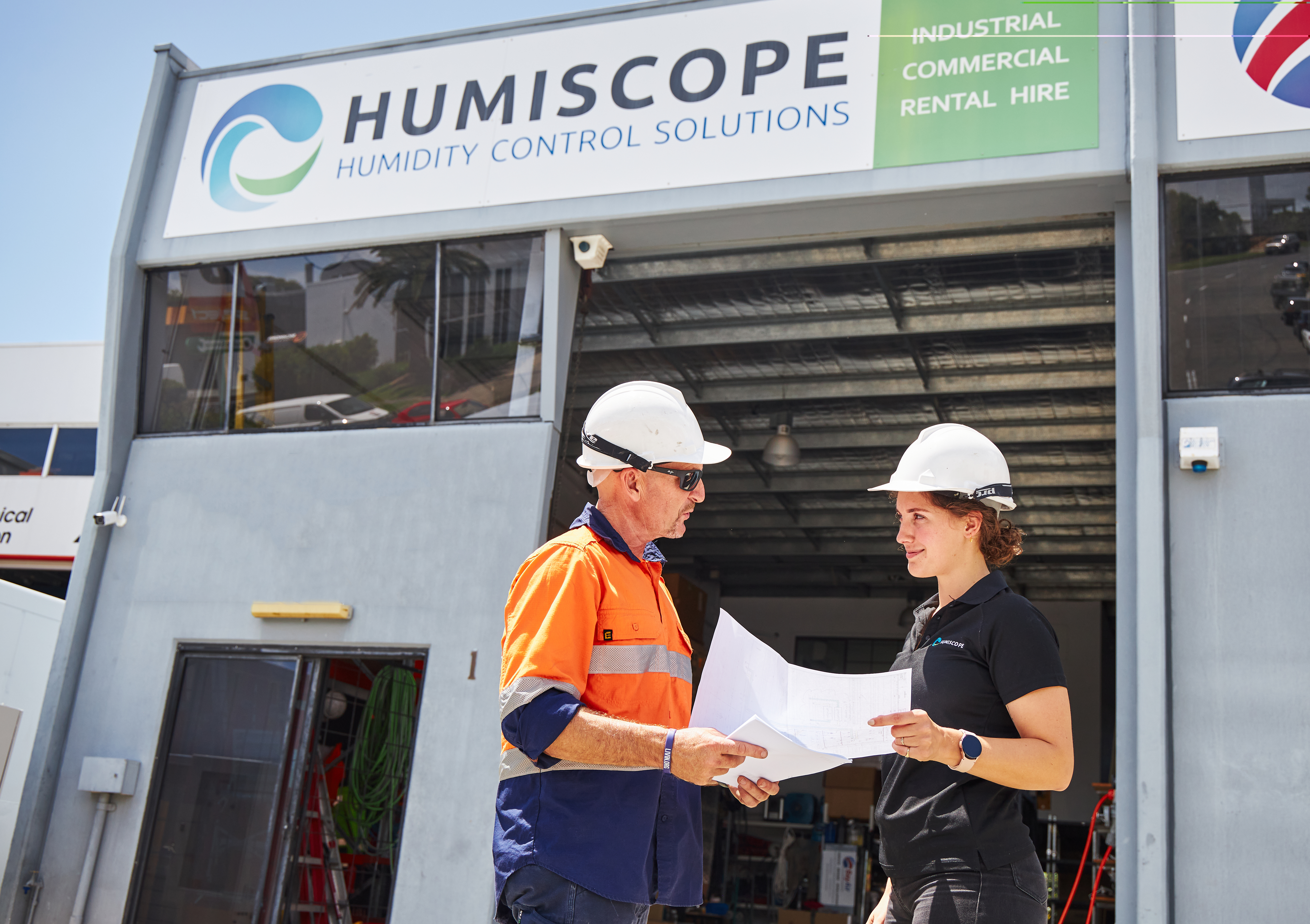
Essential Practices in Lithium Battery Manufacturing
Australia is the largest producer of lithium metal, producing approximately 50% of the world’s lithium as hard rock lithium concentrate. According to Statista.com, Western Australian mines produced about half the world’s lithium in 2021, at an estimated of 55,000 metric ton.
However, 95% of Australia’s mined lithium makes its way to China who, in 2021 manufactured 79% of all the lithium batteries that entered the global market .
As the majority of the world’s economies look at aggressively reducing carbon emissions, many countries are looking at ways to minimise supply chains and return manufacturing and production to home soil. And this universal shift toward a clean energy economy, has lithium classed as a critical metal and Australia fast becoming a manufacturing hub for lithium-ion batteries.
Lithium-ion batteries are the most popular battery used today. They are lighter than alkaline batteries and offer high operation voltage and high-power storage, therefore widely used as a power source for portable devices such as mobile phones, laptops, and digital cameras.
‘They can operate unhindered in extreme low temperatures, so ideal for outdoor applications.’ States Humiscope Director John Morgan. ‘They are also energy efficient and are being used to power hybrid and electric cars.’
Humiscope are a group of specialist engineers and technicians that have hands-on experience in designing and building ultra-dry lithium battery manufacturing and testing rooms.
‘When designing lithium battery production facilities, it is important to understand that lithium-ion is a highly reactive and flammable alkali mineral, and the batteries consist of several hygroscopic chemical components. These chemical components attract moisture’. continued John
‘Due to the chemical sensitivity to moisture, specially designed ultra-low dew point, ultra-low humidity, ultra-dry rooms are required to both test and manufacture lithium batteries.’
2017 saw an exponential worldwide increase in lithium production and these figures have increased year on year since , with analysts from firm GlobalData stating that lithium demand will more than double by 2024.
Interestingly 2017 also saw the Queensland University of Technology (QUT) produce Australia’s first lithium battery at its purpose-built battery testing facility, The National Battery Testing Centre (NBTC).
In late 2021, NBTC contacted Humiscope, specialists in dehumidification technology to discuss having a second dehumidifier installed as they expand their testing facility.
‘It is a technically complex process. For example, processing the lithium electrodes requires very low humidity levels – typically below 1% relative humidity (RH) and -35° C or -40° C dew point along with needing to be a low particulate environment.’ Said John
One of Humiscope’s clients, Cap-XX Australia, is a multinational, publicly listed company that design and manufacture thin, flat supercapacitors. Another highly moisture sensitive alternate energy source that requires precise ultra-low dew point, ultra-low humidity, dry environments.
‘We chose Humiscope because they provided strong customer service throughout the entire project and backed it up with thorough technical knowledge.’ Dallas Garratt, General Manager Operations, Cap-XX Pty Ltd
Humiscope’s project with Cap-XX was to convert an existing warehouse into an ultra-dry production space with a consistently maintained indoor climate of -50° to -55° C.
Over the last 12 months Australia has seen lithium battery manufacturing facilities begin production here in Australia. In 2021, Energy Renaissance based in the Hunter Region in New South Wales, became Australia’s pilot lithium-ion battery production facility.
‘Considering that Australia has significant weather variations with fluctuating humidity from region to region and at different times throughout the year, environmental control during battery production is essential. Added John
In the past 12 months Humiscope has been contacted by three separate manufacturers from three different states in Australia, each requiring a different size manufacturing facility.
‘Lithium reacts strongly with moisture. When lithium metal and water in the air mix, the reaction is exothermic (generates heat) and can lead to burning or even explosion. Moisture sealed inside the battery can react even after the battery is completed’.
‘On top of the safety concerns, ultra-low dew point air supply is necessary to maximise product yield, product quality, energy efficiency, product life and storage capacity. When lithium mixes with moisture it transforms into lithium hydroxide and hydrogen and product quality, performance, and durability can deteriorate significantly’. Said John
‘If the humidity is left unchecked, it lowers the quality of the battery. This leads to inferior performance and can cause safety concerns due to its high chances of explosion. Poor quality batteries can lead reduced performance and efficiency and issues achieving industry standards could prevail’.
N.B. Humiscope is an Australian owned and operated company whose core business is controlling indoor environments. Specialising in dehumidification technology, Humiscope has over 35 years’ experience in designing and building climate-controlled rooms and has worked with myriad industries both within Australia and overseas.
Humiscope is currently the only Australian owned company that provides an all-in-one solution for Lithium Battery Manufacturing Ultra Dry Rooms with the company seeing an exponential rise in requests for this service and product.
N.B. reference links are included in the PDF
www.humiscope.com.au